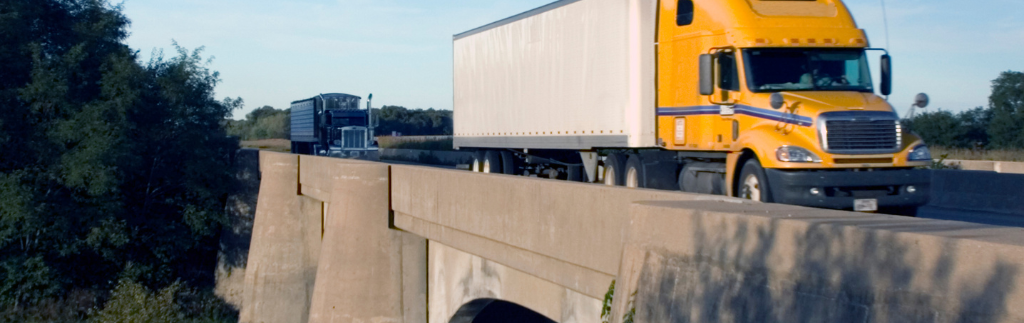
The Bridge Law was established in 1974 under the Federal Highway Act to set the maximum gross weight for a standard truck to 80,000 lbs. This law dictates how that weight is distributed in the container by setting the axle maximum limit to 12,000 lbs for the steering axle, 34,000 lbs for the drive tandems, and 34,000 lbs for the trailer tandems. So, how does this translate to payload in a container?
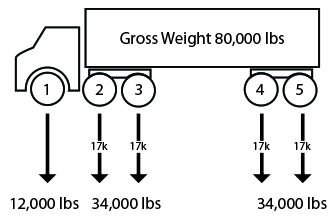
Translating to Payload
The payload is calculated by subtracting the weight of the truck, chassis, and container from the gross weight.
Gross weight (80,000 lbs) – truck (19,000 lbs) + chassis (6,700 lbs) + container (6,300 lbs) = Payload (48,000 lbs)
This gives you 48,000 lbs to work with inside a container. However, that weight must be distributed perfectly. If not, the axle maximums will be exceeded, which is why the maximum payload is often stated to be 44,000 lbs or more cautiously 42,000 lbs, depending on how uniform the load is. Setting these maximums allows cargo to be stowed evenly in the container.
What If the Cargo Isn’t Evenly Distributed?
Nose loaded containers are a common cause of weight issues on axles. Too much weight loaded in the front of the container can cause the steering axle to be lifted, which takes friction away from the front tires and creates an unsafe steering situation. It can also cause too much weight on the drive axles, resulting in overheated tires that can blow. Loading the container with more weight in the front can also cause the rear axles to be de-weighted, which reduces friction triggering issues with the rear brakes.
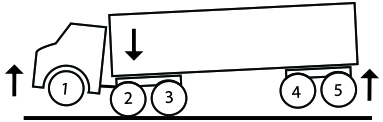
Having the weight concentrated in the nose of the container can cause serious risks for the driver while steering and braking. Internal weight distribution matters. Below are examples of how to and how not to load cargo.
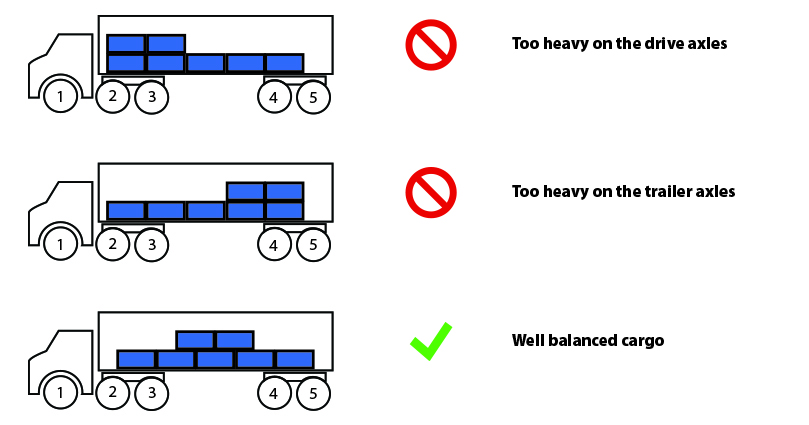
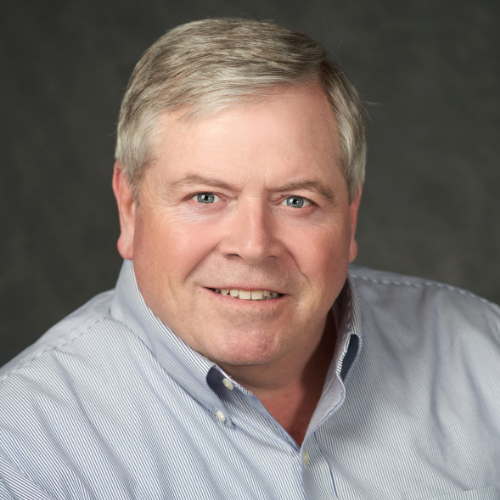